

Different approachesĪir tables have been used since the 1960s for vibration isolation, and clearly have been the most widely installed base within cleanrooms.
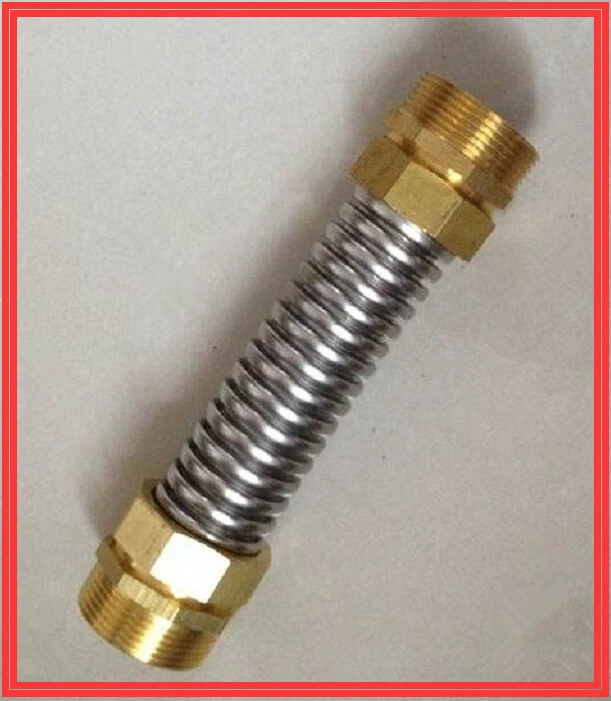
Isolator diaphragms - for compressed air tubing and electrical supply - should meet the specified outgassing, nonvolatile residue and total mass loss specifications to keep molecular contamination to an absolute minimum. Completely enclosed isolation modules and vented exhaust systems are also available to keep these workstations in compliance with cleanroom standards.Īll surfaces of the isolation table should be accessible for cleaning, and constructed so that they can be easily wiped to maintain cleanliness. Vibration isolation tables and workstations are required to meet the same cleanroom and contamination standards that the components they are protecting from vibration must meet. Used extensively in semiconductor manufacturing, biotechnology, the life sciences, and other fields that are very sensitive to environmental contaminants - such as dust, airborne microbes, aerosol particles, and chemical vapours - cleanrooms provide an enclosed environment with a controlled level of contamination that is specified by the number of particles per cubic metre at a specified particle size.Įquipment employed inside the cleanroom must be designed to generate minimal air contamination including vibration isolation equipment, which can range from relatively simple rubber blocks, metal springs and breadboards, to highly efficient air systems, active electronic systems, and negative-stiffness systems - constructed with more advanced technologies and materials for higher precision vibration isolation. But these internal and external influences primarily cause lower frequency vibrations, which are transmitted through the structure, creating strong disturbances in precision equipment used in cleanrooms.

Vibrations in the range of 2 hertz (Hz) to 20,000 Hz will influence sensitive equipment. External to the building, the equipment can be influenced by vibrations from adjacent road traffic, nearby construction, loud noise from aircraft, and even wind and other weather conditions that can cause movement of the structure. Depending on how far away the cleanroom equipment is from these vibration sources, and where in the structure the equipment is located, whether on the third floor or in the basement, for example, will determine how strongly the equipment will be influenced. Within the building itself, the heating and ventilation system, fans, pumps and elevators are just some of the mechanical devices that create vibration. Vibration can be caused by a multitude of factors. Increasingly, pneumatic air tables are taking a back seat to the more recent technology of negative-stiffness vibration isolation, which over the past 20 years since its introduction, has proven itself in thousands of applications throughout industry, government and academia, including some of the most diverse and challenging environments, such as cleanrooms. But just as technology has steadily pushed the boundaries into nano-applications in microelectronics fabrication, industrial laser/optical systems and biological research, so has the need become ever more necessary for improved precision in vibration isolation. For decades, pneumatic air tables have been the workhorse for reducing vibrations in cleanrooms for manufacturing and research, where critical micro-engineering instrumentation is employed.
